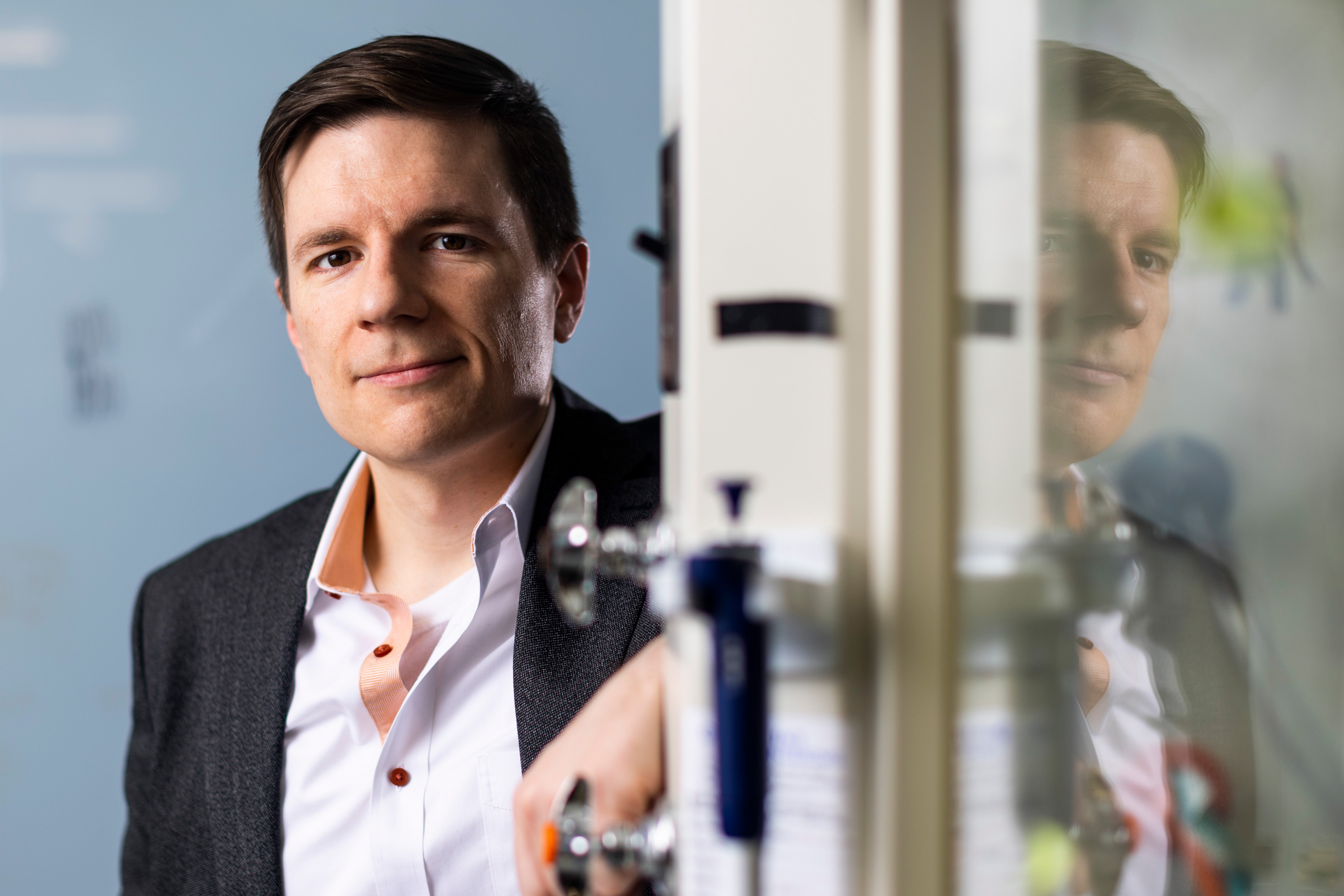
Associate Professor Robert Macfarlane is uncovering design principles that allow researchers to fine-tune materials at many size scales.
Zach Winn | MIT News Office
Some researchers are driven by the quest to improve a specific product, like a battery or a semiconductor. Others are motivated by tackling questions faced by a given industry. Rob Macfarlane, MIT’s Paul M. Cook Associate Professor in Materials Science and Engineering, is driven by a more fundamental desire.
“I like to make things,” Macfarlane says. “I want to make materials that can be functional and useful, and I want to do so by figuring out the basic principles that go into making new structures at many different size ranges.”
He adds, “For a lot of industries or types of engineering, materials synthesis is treated as a solved problem — making a new device is about using the materials we already have, in new ways. In our lab’s research efforts, we often have to educate people that the reason we can’t do X, Y, or Z right now is because we don’t have the materials needed to enable those technological advances. In many cases, we simply don’t know how to make them yet. This is the goal of our research: Our lab is about enabling the materials needed to develop new technologies, rather than focusing on just the end products.”
By uncovering design principles for nanocomposites, which are materials made from mixtures of polymers and nanoparticles, Macfarlane’s career has gradually evolved from designing specks of novel materials to building functional objects you can hold in your hand. Eventually, he believes his research will lead to new ways of making products with fine-tuned and predetermined combinations of desired electrical, mechanical, optical, and magnetic properties.
Along the way Macfarlane, who earned tenure last year, has also committed himself to mentoring students. He’s taught three undergraduate chemistry courses at MIT, including his current course, 3.010 (Synthesis and Design of Materials), which introduces sophomores to the fundamental concepts necessary for designing and making their own new structures in the future. He also recently redesigned a course in which he teaches graduate students how to be educators by learning how to do things like write a syllabus, communicate with and mentor students, and design homework assignments.
Ultimately, Macfarlane believes mentoring the next generation of researchers is as important as publishing papers.
“I’m fortunate. I’ve been successful, and I have the opportunity to pursue research I’m passionate about,” he says. “Now I view a major component of my job as enabling my students to be successful. The real product and output of what I do here is not just the science and tech advancements and patents, it’s the students that go on to industry or academia or wherever else they choose, and then change the world in their own ways.”
From nanometers to millimeters
Macfarlane was born and raised on a small farm in Palmer, Alaska, a suburban community about 45 minutes north of Anchorage. When he was in high school, the town announced budget cuts that would force the school to scale back a number of classes. In response, Macfarlane’s mother, a former school teacher, encouraged him to enroll in the science education classes that would be offered to students a year older than him, so he wouldn’t miss the chance to take them.
“She knew education was paramount, so she said ‘We’re going to get you into these last classes before they get watered down,’” Macfarlane recalls.
Macfarlane didn’t know any of the students in his new classes, but he had a passionate chemistry teacher that helped him discover a love for the subject. As a result, when he decided to attend Willamette University in Oregon as an undergraduate, he immediately declared himself a chemistry major (which he later adjusted to biochemistry).
Macfarlane attended Yale University for his master’s degree and initially began a PhD there before moving to Northwestern University, where a PhD student’s seminar set Macfarlane on a path he’d follow for the rest of his career.
“[The PhD student] was doing exactly what I was interested in,” says Macfarlane, who asked the student’s PhD advisor, Professor Chad Mirkin, to be his advisor as well. “I was very fortunate when I joined Mirkin’s lab, because the project I worked on had been initiated by a sixth-year grad student and a postdoc that published a big paper and then immediately left. So, there was this wide-open field nobody was working on. It was like being given a blank canvas with a thousand different things to do.”
The work revolved around a precise way to bind particles together using synthetic DNA strands that act like Velcro.
Researchers have known for decades that certain materials exhibit unique properties when assembled at the scale of 1 to 100 nanometers. It was also believed that building things out of those precisely organized assemblies could give objects unique properties. The problem was finding a way to get the particles to bind in a predictable way.
With the DNA-based approach, Macfarlane had a starting point.
“[The researchers] had said, ‘Okay, we’ve shown we can make a thing, but can we make all the things with DNA?’” Macfarlane says. “My PhD thesis was about developing design rules so that if you use a specific set of building blocks, you get a known set of nanostructures as a result. Those rules allowed us to make hundreds of different crystal structures with different sizes, compositions, shapes, lattice structures, etc.”
After completing his PhD, Macfarlane knew he wanted to go into academia, but his biggest priority had nothing to do with work.
“I wanted to go somewhere warm,” Macfarlane says. “I had lived in Alaska for 18 years. I did a PhD in Chicago for six years. I just wanted to go somewhere warm for a while.”
Macfarlane ended up at Caltech in Pasadena, California, working in the labs of Harry Atwater and Nobel laureate Bob Grubbs. Researchers in those labs were studying self-assembly using a new type of polymer, which Macfarlane says required a “completely different” skillset compared to his PhD work.
In 2015, after two years of learning to build materials using polymers and soaking up the sun, Macfarlane plunged back into the cold and joined MIT’s faculty. In Cambridge, Macfarlane has focused on merging the assembly techniques he’s developed for both polymers, DNA, and inorganic nanoparticles to make new materials at larger scales.
That work led Macfarlane and a group of researchers to create a new type of self-assembling building blocks that his lab has dubbed “nanocomposite tectons” (NCTs). NCTs use polymers and molecules that can mimic the ability of DNA to direct the self-organization of nanoscale objects, but with far more scalablility — meaning these materials could be used to build macroscopic objects that can a person can hold in their hand.
“[The objects] had controlled composition at the polymer and nanoparticle level; they had controlled grain sizes and microstructural features; and they had a controlled macroscopic three-dimensional form; and that’s never been done before,” Macfarlane says. “It opened up a huge number of possibilities by saying all those properties that people have been studying for decades on these nanoparticles and their assemblies, now we can actually make them into something functional and useful.”
A world of possibilities
As Macfarlane continues working to make NCTs more scalable, he’s excited about a number of potential applications.
One involves programming objects to transfer energy in specific ways. In the case of mechanical energy, if you hit the object with a hammer or it were involved in a car crash, the resulting energy could dissipate in a way that protects what’s on the other side. In the case of photons or electrons, you could design a precise path for the energy or ions to travel through, which could improve the efficiency of energy storage, computing, and transportation components.
The truth is that such precise design of materials has too many potential applications to count.
Working on such fundamental problems excites Macfarlane, and the possibilities coming from his work will only grow as his team continues to make advances.
“In the end, NCTs open up many new possibilities for materials design, but what might be especially industrially relevant is not so much the NCTs themselves, but what we’ve learned along the way,” Macfarlane says. “We’ve learned how to develop new syntheses and processing methods, so one of the things I’m most excited about is making materials with these methods that have compositions that were previously inaccessible.”