Aavash Budhathoki
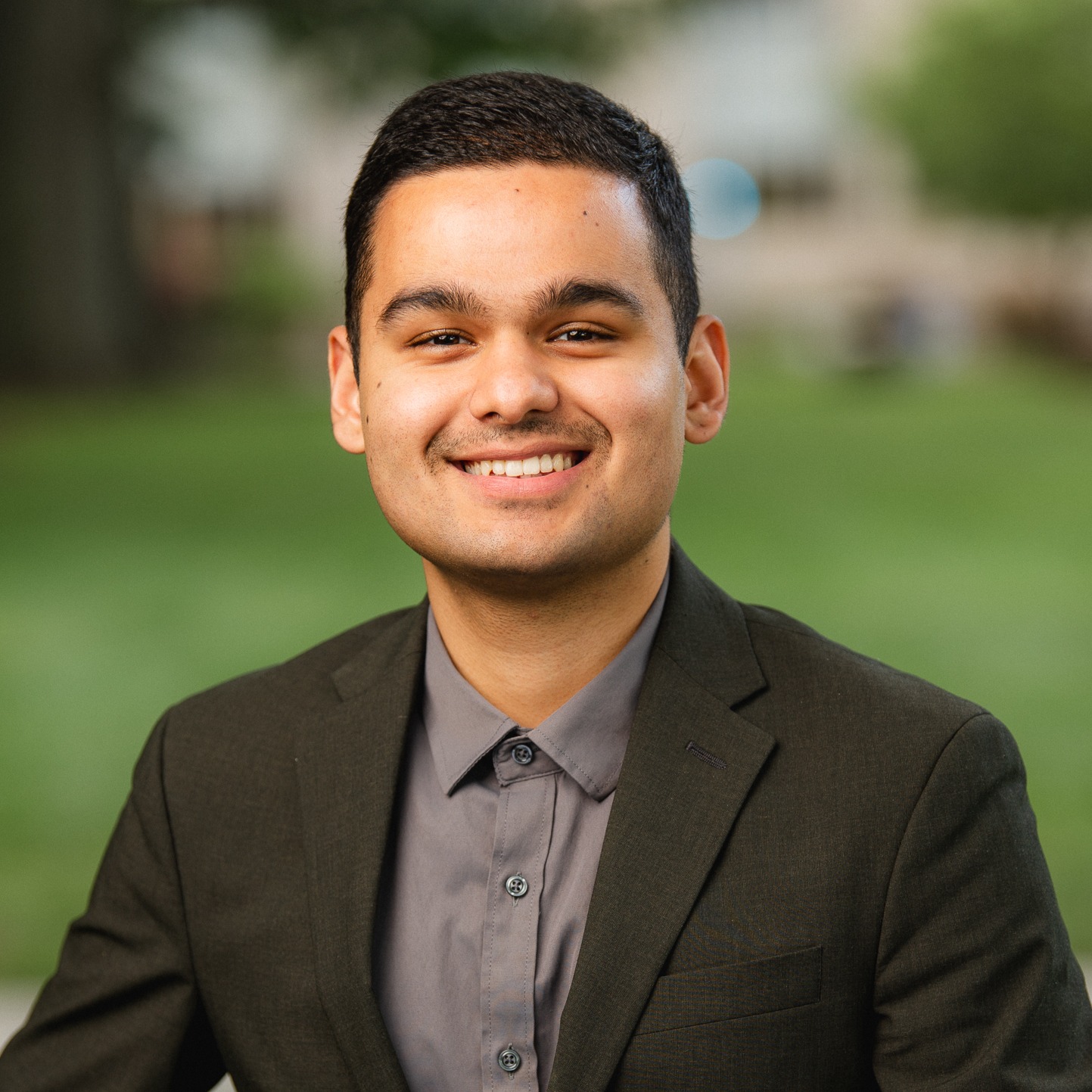
MIT Department: Mechanical Engineering
Faculty Mentor: Prof. Carlos Portela
Research Supervisor: Samuel Figueroa
Undergraduate Institution: Howard University
Hometown: Kathmandu, Nepal
Website: LinkedIn
Biography
Originally from Kathmandu, Nepal, Aavash is a rising senior at Howard University, majoring in Mechanical Engineering. He conducts research in Dr. Owolabi’s group, focusing on using additive manufacturing to produce novel materials that display superior mechanical properties. As the president of the American Society of Mechanical Engineers (ASME) Howard Chapter, he aims to foster a collaborative learning atmosphere, bringing together students from different backgrounds to conduct projects on robotics. Interested in developing and characterizing novel materials, he intends to pursue a Ph.D. in Materials Science, aiming to open up new avenues for structural, aerospace, and energy applications. At MIT, he works with Dr. Carlos Portela to study if the visco-elastic properties of additively manufactured polymers match when printed in the micro and macro scale. In his free time, Aavash can be found watching soccer, reading One Piece, or enjoying a power nap.
Abstract
Scale Independent Dynamic Behavior of Mechanical Metamaterials
Aavash Budhathoki1, Samuel D. Figueroa2, Carlos M. Portela2
1Department of Mechanical Engineering, Howard University
2Department of Mechanical Engineering, Massachusetts Institute of Technology
Mechanical metamaterials are engineered materials designed to have properties not found in naturally occurring materials. They are of interest for aerospace and structural applications due to their low weight and high tunability of static elastic properties for energy absorption. While there have been extensive studies on the response of metamaterials under quasi-static loading conditions, their dynamic properties are unexplored. Our research investigates the response of visco-elastic materials compressed at different strain rates, ranging from quasi-static to dynamic loading. We used Vat Polymerization to print photosensitive resin specimens on the macro scale, and IP-dip 2 for printing on the microscale. We recorded the response of the printed samples under compression in hopes of finding a dimensionless parameter that would closely match the stress-strain curves obtained at the different scales. Our findings will help address the question of whether the microscale architectural mechanics of metamaterials translate from the microscale to the macroscale.